This post was written by John Livermore, Executive Director of Healthy Home Healthy Planet.
Have you ever wondered how your house affects the planet? As Henry David Thoreau said, “What’s the use of a house if you haven’t got a tolerable planet to put it on.” Several years ago, I began thinking about what kind of world we’re leaving to our children, and my personal responsibility for that world. I began soul searching on how to deal with my increasing awareness about the climate crisis, and my desire to take control of my family’s carbon emissions. I knew that in order to transform my feelings of being overwhelmed into a sense of empowerment, I needed to do something significant. So I decided to take our home, a wasteful energy consumer and carbon polluter, and turn it into an energy producer.
It seemed like a marvelous idea – but there were challenges. There were only a handful of examples of homes in the U.S. that had been renovated to achieve ‘net positive energy’. I was also a single dad living with my two young daughters and 93-year-old father. And finally, I had a modest budget of just $60,000 to complete the entire renovation. Like Thoreau, when he built his cabin in the woods, we would need to be creative and do a lot of the work ourselves to create our inexpensive sustainable home.
Having such a small budget helped refine our renovation strategy to three key objectives: make it affordable, make it feasible – use off-the-shelf technologies, and make it replicable. To address the issue of few project examples, I went to one of the top energy engineers in the country, Marc Rosenbaum, and we worked together to design the project details. Once the renovation specifications were set, I assembled a small project team consisting of two friends, a carpenter, and a construction specialist, and then took a month off of work.
Before we could begin work on the house, we had to get a building permit from the city building inspector. He was skeptical of our plan, and requested a letter from Marc guaranteeing that the house would not fall down. After much discussion, we got our building permit and the tentative support of the building department.
First, we performed some diagnostic testing. An infrared scan, a way to make invisible energy use visible, showed us the many areas where we needed a lot more insulation, and a blower door test pointed out where the big air leaks were.
We designed a system that would allow us to install spray foam insulation directly on the outside walls of the house. First we did two things to prepare – extending out the gable ends of the roof to create an overhang, and extending out the piping for the water spigots and the gas meter. Then we constructed wall trusses and attached them directly over the existing siding to minimize construction waste. Once the trusses were in place, our insulator sprayed 5 inches of closed-cell foam on the outside walls of the house. The spray foam more than tripled the insulation value of our walls, from R-13 to R-43.
Around this time, my friend and ‘This Old House’ TV host Kevin O’Conner dropped by to check in on our progress. He knew that being out on the cutting edge often means getting cut. After assessing the progress of our ‘yellow cake’ he gave us a thumbs up to keep charging ahead.
In the attic, we air-sealed all the gaps that our blower door test had identified. Air sealing is a low-cost energy measure with big benefits, as it increases comfort and decreases energy bills. The conventional thinking with insulation levels is to stop once you reach a point of diminishing returns. We broke through the ‘payback’ paradigm and brought our attic insulation level up to R-76. Since we had the insulator there already, it was easy to just add more cellulose insulation. This helped us to reduce our heating load so low that we could heat the entire house with our small wood stove. We also dramatically reduced our cooling load and increased our comfort by installing a radiant barrier in the attic between the roof rafters. We haven’t turned on the air conditioner at all since completing our renovation.
In the basement, we used a simple system to insulate the concrete floor and foundation walls: moisture blocking paint, a wood frame, and foam board. Then we simply created a new floor with painted plywood and new walls with sheetrock, and presto – a finished comfortable space.
Our original windows were miserable – leaky, single-pane, double-hung, with rattly aluminum storms. Regardless of the room temperature, sitting next to a window was always uncomfortable. We replaced them with triple-pane R-5 high-performance windows. The improvement in energy performance and comfort is phenomenal. While new windows were the biggest ticket item in our renovation, they were essential to achieving our energy and comfort goals.
With a very well insulated and draft-free house, it’s extremely important to provide fresh air to the people living there. We simply upgraded our bath ventilation to a high-performance fan with a 24-hour timer. Now we all breathe fresher air and it’s easy to keep good relative humidity levels in the house. And we get fewer colds and viruses – we’re all healthier.
We discovered that it was going to be difficult to get to ‘net positive energy’ solely by upgrading our home’s building components; we would need to re-think how we used energy in the house. So, for three months we turned our home into the ‘Livermore-Gloucester Laboratory’ – a place to experiment with ways to further reduce our carbon footprint. After trying various energy use reduction strategies, we decided that air drying our clothes would produce the biggest carbon and energy savings (about 15% of our annual electricity use). So we unplugged our dryer and gave it away.
We were able to cut our energy use and carbon pollution by more than half, through LED lighting, Energy Star appliances, and behavioral changes. Then we added the tools to allow us to produce our own clean energy: solar electric and solar hot water panels.
The solar electric system provides almost twice the amount of electricity our home uses, there’s a rolling credit on our monthly account, and we’ll never pay another electric bill. Our solar hot water system provides almost 70% of our annual hot water needs, and our low-flow showerhead means we could theoretically take a 2-hour shower on one tank of solar hot water. Federal and state tax credits and utility incentives helped to reduce the cost of both solar systems.
One of the most satisfying experiences during the renovation was the evolving reactions of our neighbors. When I explained the project to them prior to construction, they looked at me like I had three heads. As the truss walls began to take shape and the spray foam was installed, several of them came over and said, ‘Wow, now I get it! This is great!’
Our project was a lesson in being bold, in not being afraid to try new things. We were able to keep the cutting edge bleeding to a minimum, and we transformed a wasteful energy consumer into a positive energy producer, a suburban clean energy power plant, on a modest budget. In addition to the dramatic energy savings, we zeroed out our home’s carbon footprint, stopped paying energy bills, increased our comfort, improved our health, and became the first renovated home in Massachusetts to produce more energy than we use. We have prepaid our energy costs for the lifetime of our home, and increased our property value by at least $20,000 to $40,000. Our project also helped to change the paradigm of what’s possible in residential energy renovations – many of our neighbors have upgraded their energy efficiency and now have solar systems too.
The best part about our project is that it is replicable. With a modest budget, some design assistance, and a little time and help from your construction-savvy friends, you can transform your house into an ultra-comfortable, low-cost, clean energy-producing home that your family will enjoy for many years. And if you are like me, you won’t miss paying those utility bills.

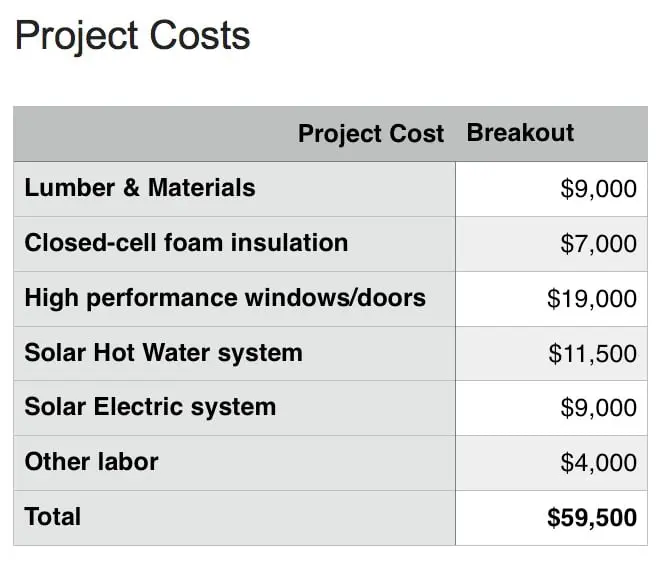