Structural Insulated Panels (SIPS) and Insulated Concrete Forms (ICFS) Framing and Insulation All in One
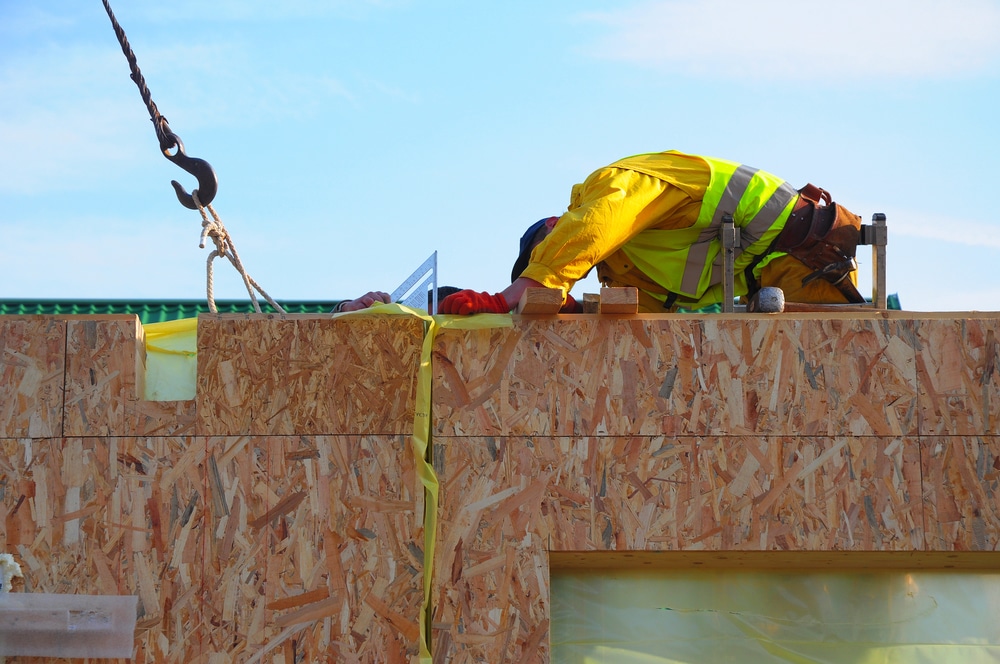
Before we get to this week’s pro term, mini-lesson, and quiz, I want to clarify something from last week’s mini-lesson on spray foam and rigid foam insulation. I said that spray foam insulation is resistant to insects and rodents, and that’s what many spray foam insulation companies say too. In that insects, like termites, are not attracted to foam insulation like they’re attracted to wood, both spray foam and rigid foam are resistant to insects.
But, there have been reports of ants and termites tunneling through spray foam and rigid foam insulation so they can GET to wood framing.
To improve insect resistance, you may want to look into rigid foam insulation that has been treated with termite resistant boric acid. In my research, I haven’t come across any spray foam insulation that contains a pesticide, but if you know of one, let us know by leaving a comment.
You could also consider treating the areas around and under the home with pesticides.
Termite inspection strips are another option. A termite inspection strip is a visible section of the concrete foundation that’s not covered by foam insulation. The inspection strip allows you to more easily see any potential termite damage. Talk to an experienced insulation installer, a home energy rater or building inspector about what termite precautions should be taken in your region if any.
Now, let’s get to this week’s pro term.
It’s chase, also called a wiring chase or electrical chase or a wall chase.
A chase is basically a channel or tube that can be strategically placed in your walls. The chase allows a number of cables or wires to run together through the walls. A chase often runs from one open space to another. For example, it might run from a crawl space to the attic. It’s very similar to a conduit, but a chase is larger.
So the pro term this week is chase, a channel that runs through a wall so that wires and cables can be routed through it.
Let’s move on to this week’s mini-lesson.
Structural insulated panels, or SIPs, are not a new product. They’ve been around for decades. SIPs are made of a core of foam insulation sandwiched between two pieces of rigid sheathing, most often oriented strand board or OSB. The panels are air sealed and provide structurally sound framing and insulation, all in one. SIPs can be used for walls, roofs, and floors. They can be used in place of, or in addition to, traditional stick framing. So, you may decide to build a traditionally framed wall system, but combine that with a SIPs roof, or vice versa. You could combine a SIPs wall system with a roof made of traditional wood trusses.
SIPs are factory made, so they can be assembled on-site faster than a house can be traditionally framed and insulated. How much faster? Well, with SIPs, the exterior walls of an average 2000 square foot house can be assembled in just 2 to 3 days. Fully insulated walls will be in place and ready for windows. While it takes weeks to months for houses to be traditionally framed, it takes only days for SIPs framing. And because SIPs are manufactured in a factory, fewer framing materials are wasted.
The R value of the SIPs will vary with the panel thickness and the type of foam used in the core. Polyurethane foam has the highest R-value at about 6 per inch and it’s also the most expensive choice. SIPs panels typically range from 4 to 12 inches thick.
Some SIPs manufacturers say that the cost to build a house with SIPs will be only slightly higher than building a traditional stick-framed house. Here’s why:
- SIPs are pre-insulated, so there’s no need to purchase additional insulation.
- You’ll save on labor costs. You could save 20-30% on framing labor since SIPs are fabricated in the factory, precut and ready to assemble when they are delivered to the job site.
- SIPs allow for a tighter, more energy efficient house which means you can often get away with purchasing a smaller, less expensive HVAC system.
- You’ll have reduced heating and cooling bills over time since the home will be so well insulated and air tight.
- Because the house goes up faster, you’ll be paying less interest on your construction loan.
- You may qualify for federal and local tax incentives by using SIPs.
Non-financial advantages of the factory made SIPs are that they are made to be perfectly straight, without the sagging or bowing that you can sometimes get with dimensional lumber. So, installing windows, doors, and millwork is faster and easier. SIPs are also more resistant to earthquake and storm forces than stick built homes.
Because they are made with sheets of OSB or plywood, SIPs provide a continuous nail bed for attaching exterior siding or interior finishes, like drywall and molding. A bonus benefit here is that you’ll never have to search for a stud again when you’re hanging pictures in your new home.
Now, this last one is a big advantage… most structural insulated panels have a warranty. Ever heard of a warranty on the dimensional lumber used for traditional stick framing? I didn’t think so.
Some disadvantages of structural insulated panels are that many builders and subcontractors are intimidated by SIPs because they’re unfamiliar with them. Some subs will even refuse to bid on a SIPs house.
Other challenges with SIPs are that special tools, and sometimes cranes are needed for framing.
SIPs can incur termite and moisture damage, so make sure you select a product treated with boric acid, which resists insects and reduces potential mold growth.
Because they’re factory made, careful project planning and sufficient lead time are required for manufacturing and shipping the product. Lead times may need to be as long as 8-12 weeks. And house plans should be specific concerning the placement of electrical wiring and outlets because SIPs need to be manufactured with electrical chases to accommodate wiring. Some electricians, especially inexperienced ones, find working with chases difficult.
House plans should also detail the exact size and placement of windows and doors so the factory can make the SIPs with accurate cut-outs. Last minute structural changes can be pricey and time-consuming since new panels sometimes have to be ordered.
What about pipes? Pipes should be installed in interior wall panels using furring strips. Pop Quiz: What are furring strips?
We talked about furring in Episode 15 called Size matters… but so does climate. Furring or furring strips are thin strips of wood or metal that are attached to a wall and spaced several inches apart. Furring is used for many reasons, but in the case of SIPs, furring would be attached to the panels to provide an extra space for pipes.
Other disadvantages of SIPs are that they can be damaged by moisture. To avoid this problem, water resistant materials must be placed SIPs soon after they are assembled. House wrap should be used to cover the panels. Although SIPs are airtight, the house wrap will provide a drainage plane, in other words, the house wrap provides protection against moisture.
Finally, depending on how unfamiliar your region is with SIPs, you may need special engineering and code approvals. And you may have trouble finding subs who have experience with SIPs.
If you’ve decided that you want to use structural insulated panels on your new home, do some research. Not all SIPs are manufactured alike. Some have better reviews, better quality foam, and higher R-values than others.
Now moving on to insulated concrete forms, ICFs.
Like SIPs, insulated concrete forms were developed decades ago. ICFs can be used for walls, floors and foundations. This system is comprised of concrete sandwiched between two layers of foam. The foam is made into interlocking modules that are stacked together without mortar. The units lock together, like Legos, and then they’re filled with concrete. This type of construction results in a very strong, quiet, energy efficient envelope that can handle high winds and storms. ICFs are said to be up to 10 times stronger than traditional stick framed homes.
ICFs come in several variations, including straight blocks and waffle style blocks. The waffle style requires 10% less concrete that the straight forms.
Wikipedia suggests that construction costs will be about 3-5% higher with ICFs as compared to a traditionally framed home. But, like SIPs, ICFs will allow for savings during and after construction. Savings that come from, not having to purchase and install insulation, needing a smaller, less expensive HVAC system, having lower utility bills, qualifying for tax credits and having lower insurance premiums. The lower insurance is because concrete homes are so strong and they are less susceptible to fire, flood and storm damage.
It’s a concrete home, so what about wiring and plumbing? Wiring and plumbing are not a problem. The foam is thick enough that it can be grooved out and wires or pipes inserted. Then spray foam used to cover the grooves. A hot knife or electric saw is commonly used to create the openings in the foam for the pipes and wires.
And what about window and door openings? Window and door openings are measured and cut out of the foam on the job site. Installers leave openings in the walls for the later installation of windows. The openings are lined with window and door frames called bucks. Wood is the material traditionally used to build bucks, but they can also made of vinyl, foam or other materials. The buck is secured in place and concrete is poured around it.
The typical R value of ICFs range from R-12 to R-26, which is pretty good for walls in moderate or hot climates. It may not be sufficient, though, if you want to build an especially high-efficiency home in a cold climate. If you really want an ICF home, and you’re building in a cold climate, some designers suggest adding exterior rigid foam insulation to ICFs.
Here’s another reason that ICFs might not be the best choice for very cold climates. The ICF wall has half of its insulation on each side of a concrete core. The concrete acts as a thermal mass, which means it can absorb and store heat. So once the heat gets through one side of the insulation, it hits concrete. Because concrete is a thermal mass, it absorbs and transfers a large amount of that heat to the ground. This is great if you live in a hot climate, where you want the heat to stay out of the house. But it’s not so good in a cold climate.
One the main challenges with ICF assembly is blowouts. The term “blowout” is used to describe the rare situation where the concrete blows out of the form. Blowouts usually occur where a damaged form has been installed, where exterior bracing is inadequate, or when the concrete is not poured at an appropriate rate.
Most blow outs are due to operator error, so hiring a concrete company and ICF installer with lots of experience will decrease your chances of a blowout. But if a blowout occurs, don’t panic because it can usually be repaired.
Both SIPs and ICFs systems are typically used for exterior walls, not interior walls. It’s not that those systems can’t be used for interior walls, but building exterior and interior walls with SIPs or ICFs would be very expensive. Most interior walls in single family homes don’t need the amount sound proofing and thermal insulation that SIPs and ICFs provide. Most people combine exterior SIPs or ICF systems with interior stick framing. You can add fiberglass or mineral wool insulation to interior walls for extra sound proofing.
Finally, if you’re like me, you’re wondering about the design limitations of using SIPs and ICFs. Although curved walls can be achieved with some brands of SIPs and ICFs, houses with simple, straight lines are easier and cheaper to construct. So it might be better to be limited curves and unusual angles to interior walls.
Well, that’s it for our basic mini lesson on structural insulated panels or insulated concrete forms.
What I’ve learned over the past several weeks is that there is no one insulation type that’s best for all situations. Exactly which insulation you choose is not as important as achieving the highest R value that your budget will allow. Remember that insulation is an investment that you will start paying you back as soon as you move into the home.
I hope you found this show helpful. If you did, you can subscribe to the podcast so new episodes will automatically be downloaded to you. If you’re listening in iTunes, there’s an icon at the bottom right of the screen that will allow you to subscribe or share the episode. Just tap the 3 small dots at the bottom right of the screen.
Before we end today’s show, let’s see how you do on this week’s quiz.
QUIZ:
1. This is the name of the channel or tube that’s strategically placed in walls that allows cables or wires to run through the walls.
A. Chase
B. Base
C. Wire Face
D. Crawl space
The answer is A, chase. A chase is like a conduit, but its bigger and it’s used to route wires and cables through a wall. SIPs use chases for electrical wiring.
2. True or False. The R value of SIPs depends on the thickness of the panel and the type of foam used in the panel core.
That’s true. Different manufacturers will use different types of foam in the core of the structural insulated panel. Polyurethane foam has the highest R value. And SIPs range from 4-12 inches thick.
3. Although SIPs and ICFs might be more expensive to build than traditional stick framed homes, which of the following are ways that you can recoup the added expense of these systems?
A. Requiring a smaller, less expensive HVAC system
B. Lower utility bills
C. Lower labor costs
D. Lower insurance premiums
E. All of the above
The answer is E, all of the above. Because SIPs and ICFs are so energy efficient, you need a smaller, less expensive HVAC system and you’ll have lower utility bills. Both SIPs and ICFs are quicker and easier to assemble. It takes days to frame a house with SIPs or ICFs, as compared to weeks or months with stick framing. So, framers spend less time on the job site, which means lower labor costs. And because these systems are stronger and more resistant to storm damage than stick framed homes, insurance premiums are usually lower.
Please remember that the purpose of this podcast is simply to educate and inform. It is not a substitute for professional advice. The information that you hear is based the only on the opinions, research, and experiences of my guests and myself. That information might be incomplete and it’s subject to change, so it may not apply to your project. In addition, building codes and requirements vary from region to region, so always consult a professional about specific recommendations for your home.
Thank you for stopping by today. I hope you’ll come back next week for the another episode of Build Your House Yourself University (BYHYU).